When you’re planning a project that requires custom welded steel structures, the last thing you want is a surprise bill. Whether you’re building an industrial framework, a large support beam, or even a custom steel enclosure, understanding how much your project will cost and how to budget for custom welded steel structures is crucial. As a manufacturer with years of experience in machining and welding, I’ve helped countless clients manage their budgets for custom steel fabrication. In this article, I’ll break down the key factors that influence the cost and share some budgeting tips that will help you get the best value without sacrificing quality.
Key Factors That Affect the Cost of Custom Welded Steel Structures
1. Material Selection: Quality Matters
Choosing the right material is the first step in determining the cost of your custom welded steel structure. Not all steel is created equal, and the material you select can significantly affect the price. You’ll typically find options like carbon steel, stainless steel, and alloy steel, each with its own price point and suitability for different applications.
A Quick Story
I once worked on a project where a client initially requested stainless steel for an outdoor structure, assuming it would offer the best durability. After discussing the project in more detail, we found that a galvanized carbon steel would actually provide the same level of corrosion resistance at a much lower cost. By making this change, we helped the client save a considerable amount while still ensuring the structural integrity they needed.
When you’re deciding on the material, think about the environment in which your custom welded steel structure will be used (outdoor vs. indoor, exposure to chemicals, etc.) and your budget constraints. Different grades of steel come with various cost differences, so it’s worth working closely with your fabricator to select the right material for your specific needs.
2. Design Complexity: Simple vs. Intricate
The complexity of your design plays a huge role in cost. Custom welded steel structures often require additional time for engineers to develop and for welders to execute, which increases labor costs. If your project involves intricate welds or unique shapes, price could be higher.
Working with an experienced fabricator can help you find ways to keep the design unique without driving up costs.
3. Size and Weight of the Structure: Bigger Isn’t Always Cheaper
It’s no surprise that larger custom welded steel structures require more material, more welding, and ultimately more labor to complete. However, this isn’t just about the size of the components; it’s also about their weight. Heavier pieces can be more difficult to handle, especially when it comes to transportation and installation.
4. Welding Process and Labor: Expertise Drives Quality and Price
The welding process you choose and the expertise of the welder can have a big impact on cost. Common welding methods include TIG (Tungsten Inert Gas), MIG (Metal Inert Gas), and stick welding. Each method has its own benefits and price points, and some may be more suitable depending on your project’s needs.
Depending on your project, it’s important to balance the quality and precision of the welding process with your budget. It’s always a good idea to discuss your options with the fabricator to ensure you’re choosing the best method for your needs.
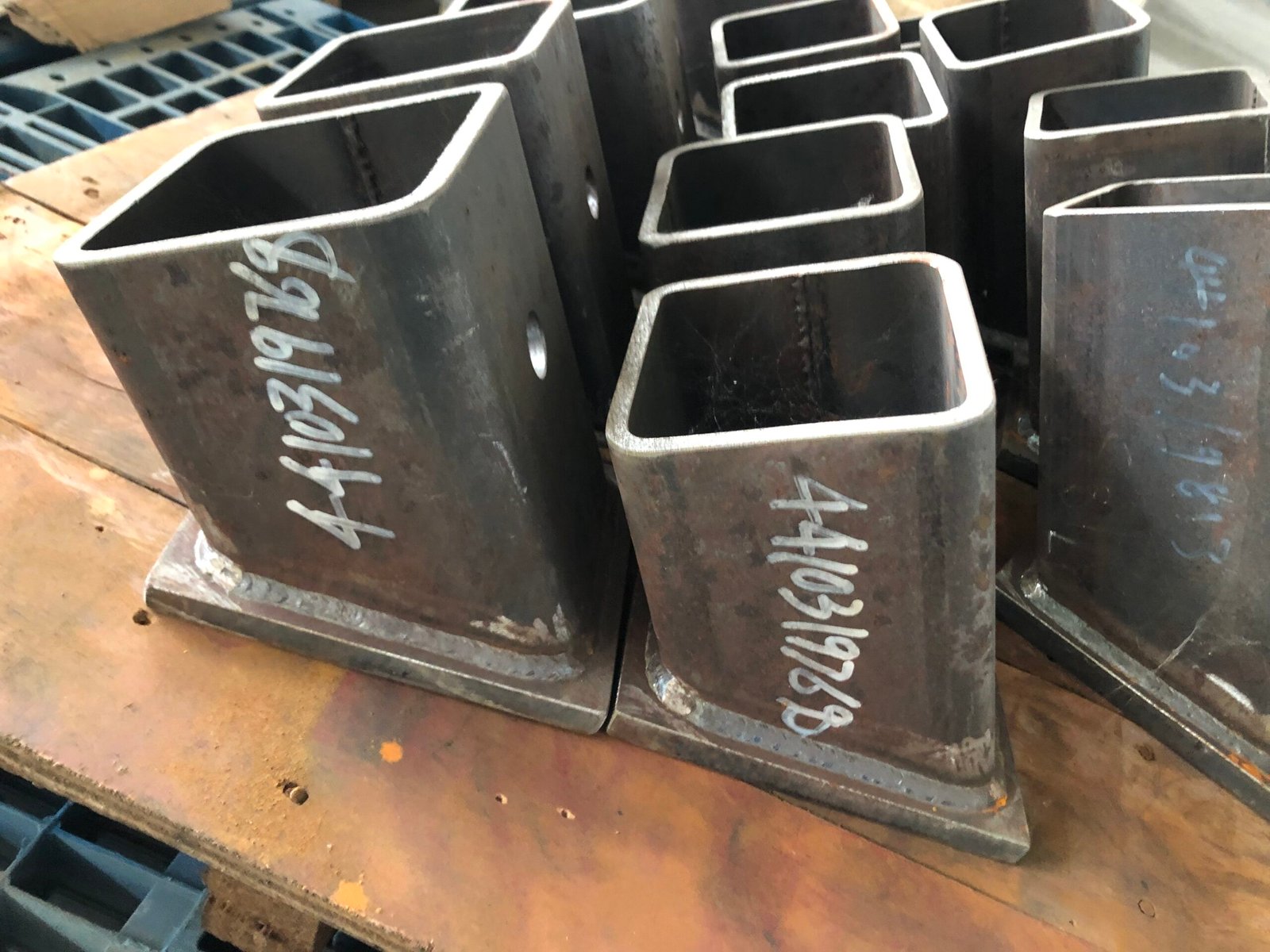
5. Lead Time and Scheduling: Rushed Orders Cost More
Urgent orders often come at a premium. Custom welded steel projects require time for fabrication, and sometimes, rushing the process can result in higher costs. If you have a tight deadline, expect to pay extra for expedited services.
If you’re working on a tight timeline, it’s essential to discuss lead times upfront with your fabricator to avoid unexpected costs. Ideally, plan ahead to allow enough time for fabrication without requiring overtime or rushed orders.
6. Post-Fabrication Processes: Additional Costs for Finishing
Once the steel has been welded and fabricated, there are usually additional processes like painting, galvanizing, or powder coating to improve durability and appearance. These finishing steps can add to the overall cost, depending on the complexity and type of treatment you choose.
For instance, galvanizing a steel structure adds a layer of corrosion protection, but it can be an additional expense. On the other hand, a simple powder coating may be more affordable, but it still comes with its own cost. It’s important to consider how your choice of post-fabrication treatment impacts both the appearance and the long-term durability of your steel structure.
How to Budget for Custom Welded Steel Projects
Now that you understand the factors that impact cost, here’s how you can budget effectively for your custom welded steel project.
1. Estimating Material Costs
Start by estimating how much material you’ll need for your project. Typically, fabricators can help you figure out how much steel will be required based on the design and dimensions of the structure.
2. Labor and Welding Costs Breakdown
Labor is one of the largest expenses in any custom welding project. The number of welding hours will depend on the complexity of the design, the size of the structure, and the welding process used. Be sure to request an itemized quote that includes labor costs so you can accurately estimate the total cost of the project.
3. Additional Costs to Consider
- Transportation Costs: Depending on the size and weight of the steel, transporting it to the fabrication shop or to your project site can be expensive. Be sure to ask about any shipping or handling fees upfront.
- Equipment Rentals: Some custom welding projects may require special equipment, such as cranes or large cutting tools. Factor these into your budget.
4. Contingency Budgeting
Even the best-planned projects encounter unexpected costs. It’s a good idea to set aside a contingency fund (usually 10-20% of the total budget) to cover unforeseen issues like design changes or material price increases.
Tips for Reducing Costs Without Sacrificing Quality
1. Source Materials Wisely
Work with your fabricator to source the best materials at competitive prices. Buying in bulk or choosing more affordable materials for certain components can save you money.
3. Efficient Welding Techniques
Choosing the right welding method and ensuring it’s done efficiently can reduce labor costs. Opt for welding methods that offer a good balance between precision and speed.
4. Plan for Long-Term Durability
Choosing durable materials and treatments may cost more upfront but can save you money in the long run by reducing maintenance and replacement costs. It’s worth investing in the longevity of your custom welded steel structure.
Conclusion
Custom welded steel structures offer flexibility and strength, but understanding the factors that impact cost is crucial for budgeting effectively. From material selection to welding processes, the choices you make will directly influence your project’s final price. By planning ahead, simplifying designs, and working with a trusted fabricator, you can ensure your project stays within budget while meeting all your needs.
If you’re ready to get started, don’t hesitate to reach out to us for a personalized quote or advice on budgeting for your custom welded steel project. With the right planning and the right team, you can achieve a high-quality result that’s both cost-effective and durable.