Ceramic Materials
Ceramic materials possess a range of excellent properties, such as being lightweight, high-temperature resistant, electrically insulating, high ablation energy, corrosion-resistant, chemically stable, wear-resistant, and vibration-resistant. Our components are ideal for environments that require protection from high temperatures, wear, or corrosive media. Anchorcut provides high-quality precision ceramics to meet customers’ research and development, as well as production needs. These materials are particularly suitable for applications in the following industries:
The primary materials we use include:
We have extensive experience with these materials and are supported by a team of experts who can help our clients develop ideal solutions tailored to the needs of each industry.
- Alumina (Al₂O₃)
- Boron carbide (B₄C)
- Boron nitride (BN)
- Graphite
- Silicon carbide (SiC)
- Silica (SiO₂)
- Silicon nitride (Si₃N₄)
Anchorcut is a leading manufacturer of tungsten carbide solutions, with products widely used in can manufacturing, aerospace, automotive, pumps and seals, oil and gas, metal forming, metalworking, and sanitary products.
We specialize in producing a wide range of wear-resistant products, parts, and stamping dies made from various materials for different industries. Our expertise lies in precision machining of materials such as Kovar alloy, tool steel, copper-tungsten, tungsten carbide, and sintered materials.
To maintain and enhance the strict precision levels we often achieve, our tungsten carbide division is equipped with specialized tools and machinery, as well as in-depth knowledge of specialized coolants and lubricants specifically for hard metals and special metals.
Our core capability lies in providing exceptional technical support to our customers and producing top-quality products through the outstanding skills and experience of our award-winning team.
Powder Preparation and Pressing/Forming
Machining prior to sintering is referred to as green machining. To minimize grinding, adding green machining before sintering is an economical process. Post-sintering ceramics/tungsten carbide are extremely hard, making their machining expensive, difficult, and time-consuming.
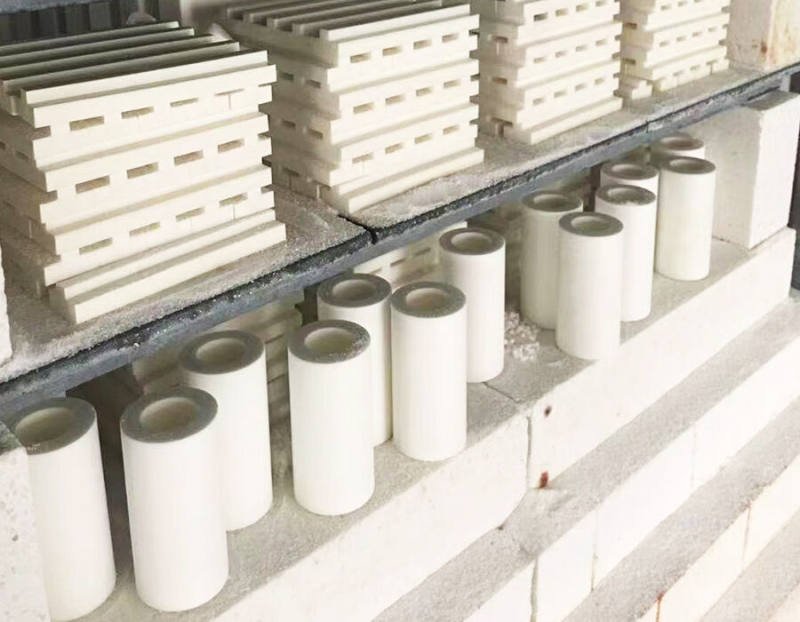
Dry pressing uses steel or carbide tooling to create “net or near-net” shapes. The process involves filling the tooling with powder and applying uniaxial pressure to compress the powder.
High-pressure injection molding for ceramics/tungsten carbide is similar to the process for other materials. Injection molding is mainly used for highly complex or high-volume components. Although the cost of injection molds is high, the per-piece cost decreases when amortized over large production runs.
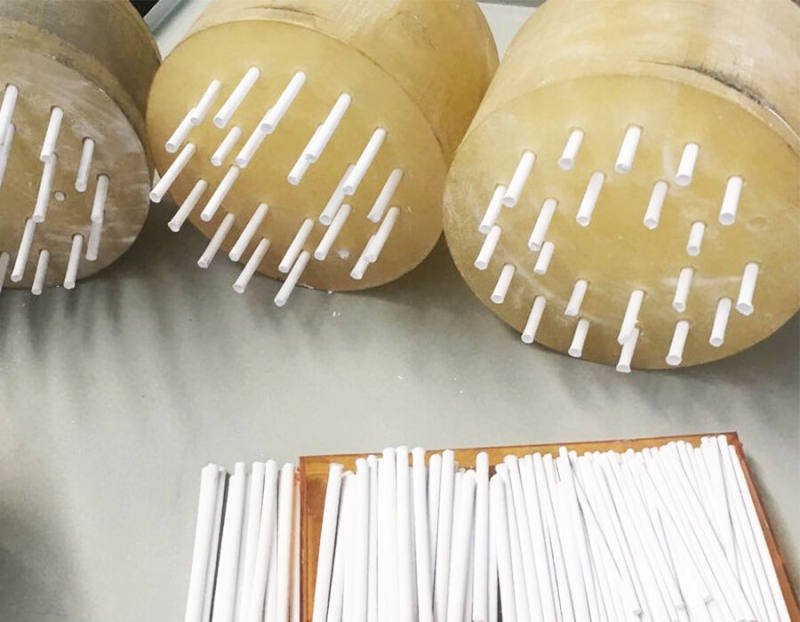
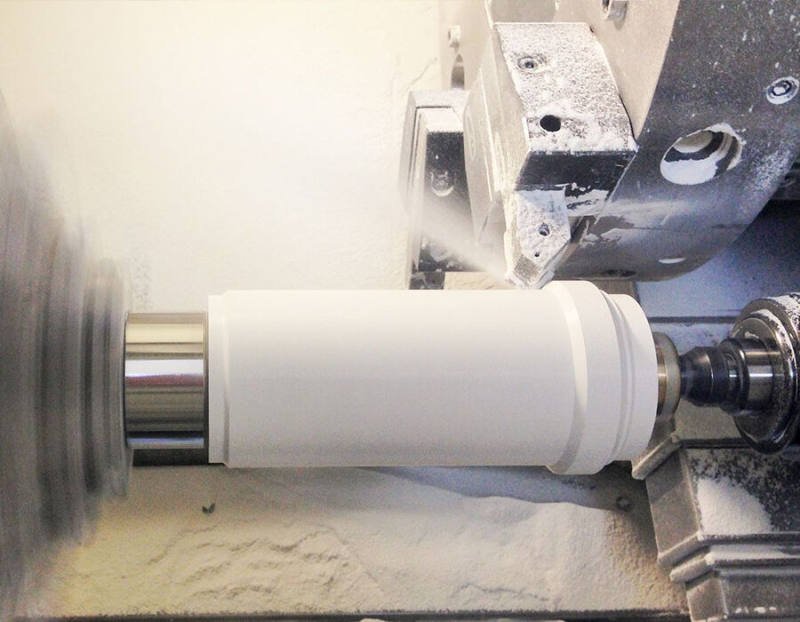
Machining prior to sintering is referred to as green machining. To minimize grinding, adding green machining before sintering is an economical process. Post-sintering ceramics/tungsten carbide are extremely hard, making their machining expensive, difficult, and time-consuming.
It is advisable to perform as much pre-sintering machining as possible because post-sintering machining is costly. The extreme abrasiveness of ceramics and tungsten carbide requires the use of carbide and PCD (Polycrystalline Diamond) tools, abrasive wheels, or even custom-made ceramic tools. After green machining, the parts are prepared for the sintering process.
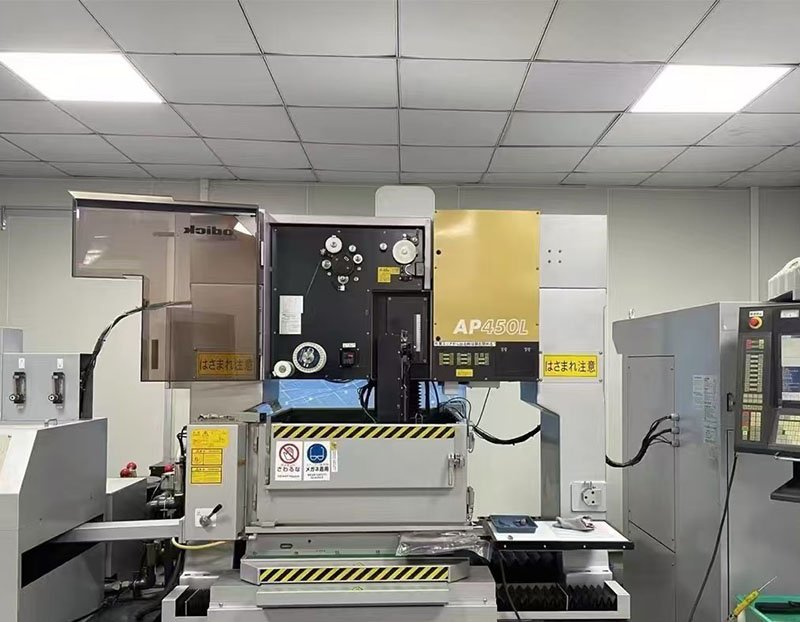
To make products hard and dense, ceramics and tungsten carbide must undergo “sintering” or prolonged high-temperature firing in a gas or electric kiln. The typical firing temperature for alumina, wood, and zirconia reaches 1600°C-1700°C. Typical sintering cycles range from 12 to 120 hours, depending on kiln type and product. Ceramics shrink by approximately 20% during sintering. The uneven shrinkage from standard forming and machining processes can lead to distortion. Our experience and knowledge in machining allow us to use specific processing and firing methods to help limit these effects.
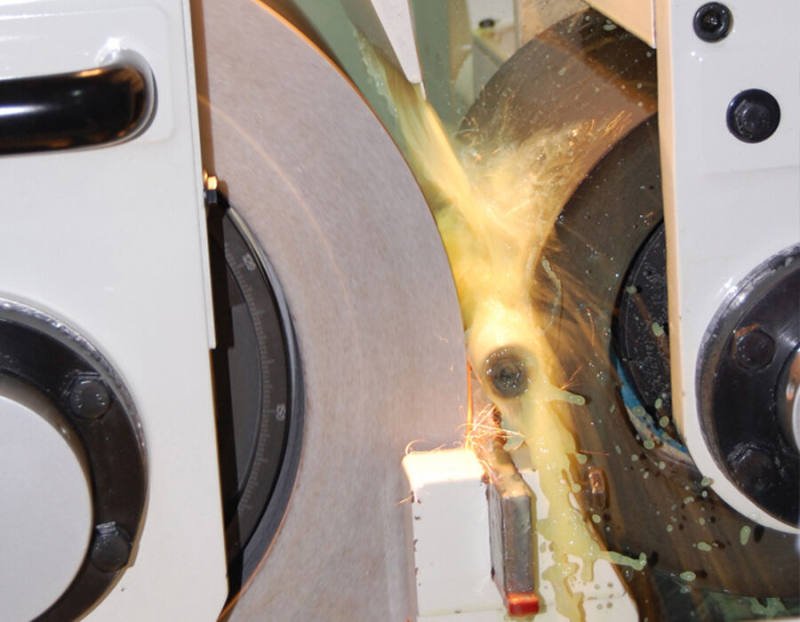
Grinding is the most commonly used method for machining sintered ceramics/tungsten carbide. Grinding operations involve rotating abrasive wheels that remove material from the workpiece surface. The grinding zone is continuously flushed with fluid coolant, which lubricates the contact between the wheel and the part surface, and removes microchips generated during the grinding process.
Diamond grinding may be required to achieve strict tolerances and surface finishes. At this stage, only diamond tools can be used, making the tooling potentially expensive. Standard machine shop equipment can be modified with plated diamond or impregnated wheels, drill bits, and various tools, along with necessary coolant recirculation and filtration systems.